Basics of Tracking Systems
Above: A dual-axis tracker made in central Ontario. This is the first production model. It is not currently available for sale.
Note that roof top tracking systems are possible, but are not common. They are not the large scale mounts that are illustrated here, but instead have a number of small positioning mounts that hold one to several panels. Currently this topic only discusses the ground mounted variety of tracking mounting systems.
Seasonal Tilt Fixed Mount
The very simplest by far of a moving system is one that is a non-motorized system that is manually switched to one of two tilt positions according to the season. The switch is done twice a year, and changes the panel tilt from about 30 degrees for the summer and to 60 degrees for the winter. With the same panel and inverter setup that I am using for my own system, located at Almonte (near Ottawa), I have analyzed the benefits of manual tilt adjustment and have concluded that this offers about a 5% increase in electricity production averaged over a year. This is based on the numbers produced by the Solar Pathfinder’s software.
The manual seasonal tilt adjustment is economical when the additional cost of the racking system is less than the value of the extra electricity generated. When the price of the panels is very high compared to the cost of the mounting system, this can provide a positive return on investment. As the price of the panels drops, at some point the benefit of buying a few more panels produces a better long term return on investment, and with a simpler and usually stronger completely fixed mounting arrangement. The other reason for doing this is when the maximum output of the system is capped, such as in the microFIT program, and the number of panels and inverter are at the maximum that is permitted, then this increases the annual output relative to a completely fixed system.
One non-monetary benefit of a seasonal tilt mount is that it sheds snow easier in the winter, and even the snow that does not drop off on its own is easier to remove with a broom.
Single Axis Tracker
A single axis tracker, which has a fix tilt for latitude, (usually 45 degrees for Eastern Ontario) and a drive system that tracks the sun in an east to west direction during the day. This motorized system can yield from 20% to 30% more electricity. The proponents of these products state that this mounting arrangement is stronger than a dual-axis mount and better able to tolerate high gusts of wind, the main enemy of all solar installations. These can have a wind sensor, and rotate in the east – west axis to park the array sideways to the wind on a windy day to protect the structure and panels. They have no “snow dump” capability.
This particular example is built similar to a swing bridge. The circular I-beam is supported by large horizontal rollers at each of the four mounting posts. Note that the supporting structure is rigidly mounted to the panel support beams at 6 places. The drive forces are transmitted by a chain, using an industrial motor and gearbox. The only periodic maintenance is to ensure that the chain remains fully greased to prevent corrosion. The missing panel is deliberate, to reduce the wind pressures that build up. This is designed to be assembled quickly, in one day, and no heavy equipment is required, except to screw the four auger mounting posts into the ground. This is the API SUN–SPY™ SST–10, made in the Barrie area. There are other similar designs using the same principle, and example is by Powertrac.
There are also "top of Pole" mounted single axis trackers on the market. Multiple instances would be required for a 10 kW system.
The following example is a Lorentz single axis tracker using a sloped beam which is oriented S - N. The amount of fixed tilt is adjustable during installation. This mount requires 3 such mounts for a 10 kW installation. It uses Shucco panels, which are recently available as Ontario Qualified content. In this example there are Enphase M380 inverters, one for every two panels. Note this inverter has been discontinued.
This tracker has 8 pivot points, and a linear activator arm. The 8 mounting points act as bearing, and provide a very robust frame. The weakest part of this design in a very high wind is the linear activator, which could be easily replaced if it was bent due to excessive wind forces. This is a German design, recently beginning manufacturing in Kingston. The frame components are all hot dipped galvanized steel.
The same company and some other companies make a smaller scale rooftop capable tracker using the same sloped main beam structure. The difference is the support is done in three places, and it would not be classified as a pole mounted system. This system readily scales down for mounting smaller number of panels. This same concept was used for large C band satellite dishes that were popular in the 1980s.
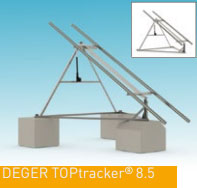
Deger makes a single axis tracker that called a top tracker 8.5 that is very easy for a DIY person to install, since it mounts at three points. It can be installed without any heavy equipment. We can supply this product! An illustration from a Deger catalog demonstrates the construction of this mount. The simplicity is the anchoring can be done onto pre cast curbs or blocks, three concrete Sonotube posts, or a variety of other foundations, since the 8m2 panel area produces relatively modest forces when spread over three anchor points. It can be installed on commercial flat roofs, where the weight of a dual axis tracker would be prohibitive.
Dual Axis Trackers
The dual axis tracker is the top performer for maximizing the electricity production from a fixed number of PV panels. The tracking keeps the panels oriented at 90 degrees to the sun, to maximize the solar energy striking the panels and therefore produces the greatest amount of electricity. The dual axis tracker has the benefit for being able to do a “snow dump” on a daily basis during the winter, and to go into tabletop parking mode during times of high wind. The snow dump features make these attractive for unattended locations.
This dual axis tracker uses a poured in place ballasted concrete mount. (No hole is required, the ground is levelled off and some gravel spread and the base is cast in place.) The red boxes are the string inverters, which will be enclosed in a temperature regulated enclosure to moderate the winter temperatures. In the background you can see the moulds that were used to pour the 13 Yards of concrete in the base. It also has gaps between rows of panels, and the middle set of panels are a few inches closer to the sun to reduce the buildup of wind forces. The next picture is of the back side of the same unit. Note: This unit is not available for sale, it is still shown on this web site as it is a good example of this type of tracker.
The red parts are a worm gear motor and gearbox to rotate the panels in the East-West direction. The rectangular component prominent in the right side of the image is the tilt motor, which is a lead screw type of linear activator. In this design, the entire weight of the panels is supported at two points, by two large bearings at the end of the Y shaped yoke.
Both single and dual axis types of trackers can use either a brightest spot tracking algorithm or an astronomical prediction model to point the panels at the sun. Some are selectable for either mode of operation. The unit pictured above is user selectable to use either method.
Here is a different brand of dual-axis tracker, Deger which has been in production in Germany for a long time. This is now available as a product with Ontario content and suitable for microFIT projects.
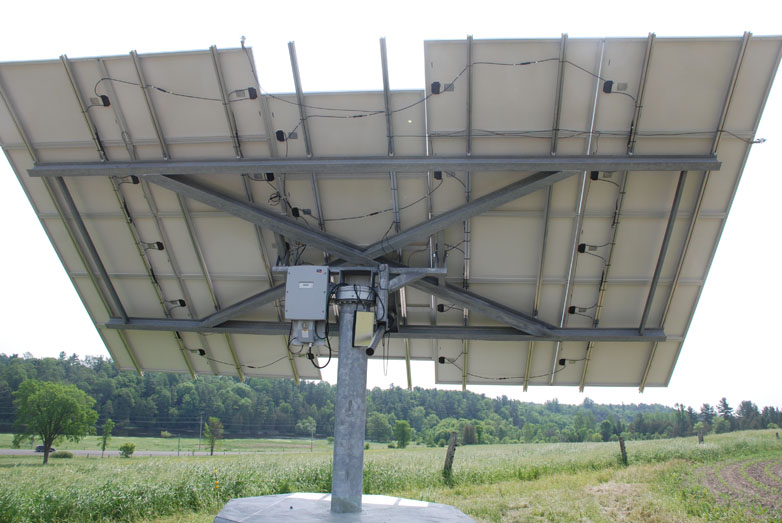
This also uses a worm gear drive to rotate in the East-West axis, and also uses a lead screw type of linear activator to apply the north-South Tilt. This uses the brightest spot sun tracking method. See the Ground foundation topic for another view of this tracker's base.
This particular installation of two trackers with 48 Canadian Solar 230W panels produced about 33% more power than my installation over an identical 2 1/2 month period in the spring of 2011. My installation is a fixed ground mounted system with 52 230W panels and the same two SMA SB5000 string inverters. This installation is located 15.5 km away in a straight line.
Use of Tracking PV Systems
The gains relative to a fixed mounting system are due to directly facing the sun throughout the day. This requires that the location of the tracker should have an unshaded view of the sky, right down to the horizon all year long. This is about a 248 degree sweep of the horizon near Ottawa. If there is any shading along this path, the gains from tracking will be reduced. An analysis with a Solar Pathfinder can determine how much reduction can be expected.
Single and Dual-axis trackers are attractive when a program such as microFIT limits the amount of capacity of the system. Without this limit, it probably is less expensive to just install more panels and inverters to increase the production by the 30 to 40% and have a no moving parts system. The other factor is the cost of the panels. The more expensive the panels, then the greater the justification of using a tracking system to maximize the output from those panels.
The OPA has stated that in their view the average cost of a tracking system in 2010 is about $25,000 more than a fixed system. (They did not discriminate between singe and dual axis mounts) The vendors of tracking systems may disagree. With time and production volume, the costs should fall.
The impact of the Ontario content rules for the racking system have the most impact on the cost of tracking PV mounting systems. Without the Ontario content rules, the trackers could be imported from countries such as Germany that have had a significant solar incentive program running for a number of years. In Ontario, nearly all of the “made in Ontario” tracker systems are relatively new, and were not in production in Ontario prior to the microFIT program introduction.
One challenge for tracking system manufacturers is the Canadian climate, which is harsher than is found in most of Europe and so systems based on those that have been proven to be reliable in Europe may not be trouble free in Ontario. This is a challenge for new Ontario based manufacturers who have introduced tracker designs motivated by the microFIT program.
Lightning protection is more critical in a tracking system because they are typically located in an open location where they are the highest object in the sky. Therefore they are more likely to be struck than a fixed ground mounted system which are lower in height and longer.
Note that all of the solar farms that I have seen so far use fixed ground mounted systems. This is a hint that indicates that the reliability and the total electricity production for the dollars invested with maintenance costs is more favourable using lower cost fixed mounting systems. In some cases, such as Galletta they lower efficiency panels with a lower cost per watt of output to get the best overall return on investment.
I would expect he reliability of key components of a PV system are approximately in the following order, from the best down to the least reliable:
- PV panels
- Inverters located indoors in a room temperature location
- Inverters located outside
- Moving components of a mounting system
Therefore I expect that a fixed system with inverters mounted indoors would be the most reliable. Anyone considering a tracking system should allocate more money for future maintenance and repairs than the owner of a fixed system. This should be factored into the overall returns of the system.
Purchasing a Tracking System
If you wish to purchase either of the first two types, I can sell you either product but only on the basis as a fully turnkey system. None of these trackers are suitable for a DIY installation. We don't do the installation, but subcontract that out to a company that specializes in installing these systems. The Deger dual axis tracker is available as a kit suitable for DIY installation. Two of the Deger 5000HD will hold a total of 860 ft of panels, and are a good choice for 10kW microFIT systems. The smaller size of the 5000HD makes this a more manageable size for DIY installers.
The Deger top tracker 8.5 is the best choice for a DIY tracker, less productive than a dual axis unit, but far more affordable, and much easier to install.